Vergussmasse für Elektronikkomponenten
Vergussmassen auf Epoxidharz- und Acrylatbasis werden in der Elektronik häufig zum Schutz von Elektronikkomponenten, Halbleitern und Baugruppen eingesetzt. So soll die Vergussmasse die Komponenten vor Feuchtigkeit, Staub, Schmutz oder Lösemitteln schützen. Auch gegen mechanische Belastung schützen Vergussmassen effektiv als Abdeckungsmasse oder als Füllmasse um Hohlräume zu vergießen.
Alle Vergussmassen von Panacol sind ohne Lösemittel hergestellt. Viele besitzen eine Ionenreinheit von <10 ppm bei Na+, K+, Cl- und Br-. Somit schützen sie optimal gegen innere Korrosion und die Lokalelementbildung wird reduziert.
Viele Vergussmassen sind UV-härtend, wodurch eine schnelle Aushärtung innerhalb weniger Sekunden erfolgen kann. Das Vergießen von Komponenten oder Elektronikbauteilen ist dadurch für eine hochvolumige und vollautomatisierte Fertigung geeignet.
Thermisch aushärtende Vergussmassen hingegen haben den Vorteil, dass sie auch in Schattenzonen, die das UV-Licht nicht erreichen kann, aushärten. Diese Vergussmassen können auch eine schwarze Einfärbung haben, um sie als Abdeckung oder Beschichtung zu verwenden.
In der folgenden Tabelle finden Sie eine Auswahl von Vergussmassen und Mold Compounds von Panacol. Weitere Produkte oder kundenspezifische Lösungen sind auf Anfrage erhältlich.
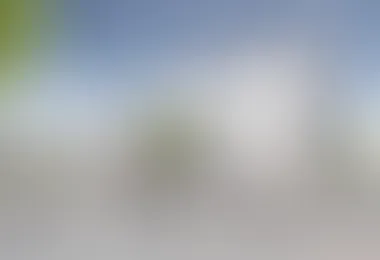
Ein schwarzer Klebstoff wird als Vergussmasse eingesetzt
Technische Datenblätter können durch Klicken auf den Klebstoffnamen heruntergeladen werden.
Vergussmasse | Viskosität [mPas] | Basis | Aushärtung* | Besondere Eigenschaften |
---|---|---|---|---|
Structalit® 5521 | 1.200-2.000 (Rheometer, 25°C, 10s^-1) | Epoxidharz | Thermisch ab 60°C |
Nicht-leitend Hervorragende Haftung auf Hochleistungskunststoffen (LCP, PBT) Hohe Reinheit (“Electronic grade standard”) Flexibel |
Structalit® 5531 | 5.000-10.000 (Rheometer, 25°C, 10s^-1) | Epoxidharz | Thermisch ab 60°C |
Nicht-leitend Hervorragende Haftung auf Hochleistungskunststoffen (LCP, PBT) Hohe Reinheit (“Electronic grade standard”) Gute mechanische Stabilität Gute Chemikalienbeständigkeit |
Structalit® 5800 | 7.000-15.000 Mix (LVT, 25°C, Sp. 4/30 rpm) | 2K-Epoxidharz |
thermisch, Raumtemperatur |
Hohe Temperaturbeständigkeit Kurze Topfzeit Schnelle Verarbeitung |
Structalit® 5801 | 12.000-22.000 Mix, 10.000-20.000 Teil A, 18.000-29.000 Teil B, (Rheometer, 25 °C, 10s^-1) | 2K-Epoxidharz |
thermisch, Raumtemperatur |
Schwarze Farbe Gute Öl-, Chemikalien- und Feuchtebeständigkeit Geringer Schrumpf Geringe Wasseraufnahme Gute Haftung auf Metallen, Glas und Kunststoff |
Structalit® 5802 | 40.000 - 65.000 Mix (Rheometer, 25°C, 10s^-1) | 2K-Epoxid |
thermisch Raumtemperatur |
Dunkelgraue Farbe Gute Öl-, Chemikalien- und Feuchtebeständigkeit Schlagzäh Geringe Wasseraufnahme Sehr gute Haftung auf Metallen Brandklassifizierung in Anlehnung an UL 94 HB |
Structalit® 5810-1 | 3.000-4.000 Mix (LVT, 25°C, Sp. 4/30 rpm) | 2K-Epoxidharz |
thermisch Raumtemperatur |
Sehr hohe Haftung auf PC Sehr gute Feuchte- und Chemikalienbeständigkeit |
Structalit® 5891 | 25.000-50.000 ( Rheometer, 25 °C, 10s-1 ) | Epoxidharz | thermisch |
Schwarze Farbe Hohe Schockbeständigkeit Kantenstabil Nass-in-nass verarbeitbar mit Füllmaterial |
Structalit® 5891 T | 80.000-150.000 (Rheometer, 25 °C, 10s^-1 ) | Epoxidharz | thermisch |
Schwarze Farbe Standfestes Frame-Material, nass-in-nass verarbeitbar mit Füllmaterial für Frame&Fill-Anwendungen, auch mit mehreren Frames aufeinander dosierbar Kantenstabil Sehr gute Schockbeständigkeit |
Structalit® 5893 | 6.000-10.000 (Rheometer, 25°C, 10s^-1) | Epoxidharz | thermisch |
Schwarze Farbe Fließfähig Als Fill verwendbar, nass-in-nass verarbeitbar mit Frame-Material für Frame-and-Fill Hohe Schockbeständigkeit Sehr gute Temperatur- und Chemikalienbeständigkeit Zertifiziert nach ISO 10993-5 |
Structalit® 5894 M | 20.000-30.000 (Rheometer, 25 °C, 20s ^-1) | Epoxidharz | thermisch |
Schwarze Farbe, fließfähig, als Fill für Frame-and-Fill-Anwendungen verwendbar sehr gute Temperatur- und Chemikalienbeständigkeit, hohe Schockbeständigkeit |
Structalit® 8801 | 30.000 - 45.000 (LVT, 25°C, Sp. 4/6 rpm) | Epoxidharz | thermisch |
Gute Öl-, Chemikalien und Kraftstoffbeständigkeit Fließfähig, beige Farbe, Kurze Härtezeiten bei niedrigen Temperaturen, Zertifiziert nach ISO 10993-5 |
Structalit® 8801 black | 30.000 - 45.000 | Epoxidharz | thermisch |
Gute Öl-, Chemikalien und Kraftstoffbeständigkeit Schwarze Farbe Fließfähig |
Structalit® 8801 T | 16.000-30.000 (Rheometer, 25 °C, 5s^-1) | Epoxidharz | thermisch |
Gute Öl-, Chemikalien und Kraftstoffbeständigkeit; Standfest |
Structalit® 8805 | 30.000-45.000 | Epoxidharz | thermisch |
Gute Öl-, Chemikalien und Kraftstoffbeständigkeit Fließfähig Beige Farbe |
Structalit® 8838 | 6.500-7.500 (Rheometer, 25°C, 20s^-1) | Epoxidharz | thermisch |
Schwarze Farbe, jetbar, fließfähig, schnelle Aushärtung, Flexible Vergussmasse Niedriger Halogengehalt, schockbeständig Niedrige Glasübergangstemperatur |
Vitralit® 1600 LV | 3.000-5.000 | Epoxidharz |
UV thermische Nachhärtung |
Hohe Glasübergangstemperatur Geringe Wasseraufnahme Sehr gute Chemikalienbeständigkeit Sehr kleiner Härtungsschrumpf Geringer Ionengehalt (<5ppm) Thermische Nachhärtung |
Vitralit® 1605 | 200-400 (LVT, 25°C, Sp. 2/30 rpm) | Epoxidharz |
UV thermische Nachhärtung |
Sehr geringer Schrumpf Geringe Wärmeausdehnung Sehr hohe Glasübergangstemperatur Hervorragende Chemikalienbeständigkeit Zertifiziert nach ISO 10993-5 Sterilisationsbeständig |
Vitralit® 1671 | 9.000-14.000 (Rheometer, 10s^-1) | Epoxidharz |
UV thermische Nachhärtung |
Standfestes Frame-Material, nass-in-nass verarbeitbar mit Füllmaterial Hohe Ionenreinheit Gute Wärmeleitfähigkeit Geringe Wasseraufnahme UL94 HB Test bestanden |
Vitralit® 1688 | 1.200-2.000 | Epoxidharz | UV |
Gute Klimabeständigkeit Geringer Ionengehalt Chipabdeckmasse Leichtes Verfließen/Nivellierung |
Vitralit® 1691 | 20.000-40.000 | Epoxidharz |
UV thermische Nachhärtung |
Schwarze Farbe Hohe Ionenreinheit Hervorragende Temperaturbeständigkeit Schnelle UV-Fixierung der Oberfläche |
Vitralit® 1722 | 5.000-8.000 (LVT, 25 °C, Sp. 4/30 rpm) | Epoxidharz | UV |
Sehr hohe Adhäsion zu den meisten thermoplastischen Kunststoffen Geringer Schrumpf Hohe Temperaturbeständigkeit |
Vitralit® 2004 F | 60-100 (LVT, 25 °C, Sp. 2/30 rpm) | Epoxidharz |
UV thermische Nachhärtung |
Fluoreszierend Flexibel Autoklavierbar Trockene Oberfläche im ausgehärteten Zustand Ionenrein Hohe Chemikalienbeständigkeit Sprühfähig |
Vitralit® 2007 F | 150-350 (LVT, 25 °C, Sp. 2/30 rpm) | Epoxidharz |
UV thermische Nachhärtung |
Fluoreszierend Flexibel Autoklavierbar Hervorragende Chemikalienbeständigkeit Ionenrein |
Vitralit® 2009 F | 100-200 | Epoxidharz |
UV thermische Nachhärtung |
Fluoreszierend Flexibel Autoklavierbar Hervorragende Chemikalienbeständigkeit Ionenrein |
Vitralit® 2028 | 160-300 | Epoxidharz |
UV thermische Nachhärtung |
Trockene Oberfläche nach Aushärtung Autoklavierbar Hervorragende Chemikalienbeständigkeit Kratzfeste Beschichtung verläuft nicht, hohe mechanische Beständigkeit |
Vitralit® 4451 MV F | 2.000-3.000 (LVT, 25°C, Sp. 4/30 rpm) | Acrylat | UV, VIS |
Weich und elastisch Schutzbeschichtung schnelle Aushärtung Trockene Oberfläche in ausgehärtetem Zustand Blau fluoreszierend |
Vitralit® 5140 | 250-500 | Acrylat |
UV VIS |
Flexibel Zertifiziert nach USP Class VI Auch gut geeignet für Kunststoffe mit geringer UV-Durchlässigkeit und Transparenz, sowie für schwierig zu verklebende Kunststoffe |
Vitralit® 5140 VT | 5.000-10.000 (Rheometer, 25°C, 10s^-1) | Acrylat |
UV VIS |
Gute Wechselklima- und Feuchtebeständigkeit Flexibel Standfest Geringer Schrumpf, optisch klar Geeignet für schwierig zu verklebende Kunststoffe |
Vitralit® 6103 | 3.500-5.000 | Acrylat |
UV thermische Nachhärtung |
Gute Haftung auf Metallen und gesinterten metallischen Werkstoffen Transparent |
Vitralit® 6104 | 3.000-8.000 | Acrylat |
UV thermische Nachhärtung |
Gute Haftung auf Metallen und gesinterten metallischen Werkstoffen |
Vitralit® 6104 VT | 8.000-17.000 (Rheometer, 25°C, 10s^-1) | Acrylat |
UV thermische Nachhärtung |
Gute Haftung auf Metallen und gesinterten metallischen Werkstoffen Ideal zur Befestigung großer Bauteile auf Leiterplatten (corner bonding) nachträgliche Aushärtung von Schattenbereichen möglich |
Vitralit® 6105 | 3.500-6.000 | Acrylat |
UV thermische Nachhärtung |
Gute Haftung auf Metallen und gesinterten metallischen Werkstoffen |
Vitralit® 6125 | 4.000-6.000 (LVT 25°C, Sp. 4/30 rpm) | Acrylat |
UV thermische Nachhärtung |
Mit Aktivator härtbar Sehr gute Haftung auf Stein, Glas, Metallen und thermoplastischen Kunststoffen Mittlere Viskosität |
Vitralit® 6128 | 800-1.200 | Acrylat |
UV thermische Nachhärtung |
Mit Aktivator härtbar Sehr gute Haftung auf Stein, Glas, Metallen und thermoplastischen Kunststoffen |
Vitralit® 6128 VT | 18.000-30.000 (LVT, 25°C, Sp. 4/6 rpm); 3.000-6.000 (Rheometer, 25°C, 10s^-1) | Acrylat |
UV thermische Nachhärtung |
Mit Aktivator härtbar Sehr gute Haftung auf Stein, Glas, Metallen und thermoplastischen Kunststoffen Hohe Temperaturbeständigkeit Hohe Viskosität |
Vitralit® 9179 | 200-400 | Acrylat | UV |
Schnell härtend Besonders geeignet für automatische Produktion Gelbe Farbe |
Vitralit® 9180 | 700-1.200 | Acrylat | UV |
Trockene Oberfläche Schnelle Aushärtung auch in tiefen Schichten Gelbe Farbe |
Vitralit® 9181 | 4.000-7.000 | Acrylat | UV |
Trockene Oberfläche Schnelle Aushärtung auch in tiefen Schichten Gelbe Farbe |
Vitralit® UD 5180 | 4.000-6.000 | Epoxidharz |
UV thermische Nachhärtung |
Graue Farbe Besonders geeignet für flexible Leiterbahnen Sehr gute Haftung auf Metallen Jetbar Reflow beständig |
Vitralit® VBB-1 | 1.000-1.500 | Acrylat |
UV VIS |
Elastisch Hohe Schälfestigkeit Optische Klarheit Hoch flexibel Vergussfähig hohe Feuchtebeständigkeit |
Vitralit® UD 8055 | 5.000-8.000 (Rheometer, 25°C, 10s^-1) | Acrylat |
UV VIS Feuchte |
Hohe Glasübergangstemperatur Schnell härtend Verträglich mit Flussmittel Niedriger Ionengehalt |
Vitralit® UD 8056 | 3.000-6.000 (Rheometer, 25°C, 10s^-1) | Acrylat | UV / VIS / Feuchte nachhärtend |
Hohe Glasübergangstemperatur Schnell härtend Verträglich mit Flussmittel Niedriger Ionengehalt UL94 HB-Test bestanden |
*UV = 320 - 390 nm VIS = 405 nm